If you discover that your wrap has a hole in it, it is first worth working through our ‘hole assessment’ post to help you decide what has caused it and what action (if any) you should take next.
This post shows you the mending process of a wrap with a flipping massive hole in it!
The Problem
The wrap that I chose to mend was 5 years old by this point, and had had 4 years of regular use. The hole had developed in the area of greatest repeated wear- slap bang in the middle of the length of the wrap and in the bottom third of the cloth. This would be the spot that baby’s bum sat on for most carries, and the cloth would stretched taut, rubbing against baby’s clothes and the leg passes of the wrap.
It shows how tough wraps really are, that they can receive the hard wearing that they do for years on end, and only rarely get to this point. Most denim jeans would have given out long ago!
The cloth had worn into a hole, but only the white, weft threads had been eroded. The blue warp threads were all completely intact. This is pretty common, as the warp threads are individually very strong. They are thin, tightly spun and plied, and there are a lot more of them. The weft threads don’t need to be as strong individually, because the ‘strength’ of the cloth overall comes from the structure of the weave and the way the threads interact, not how they work as single strands.
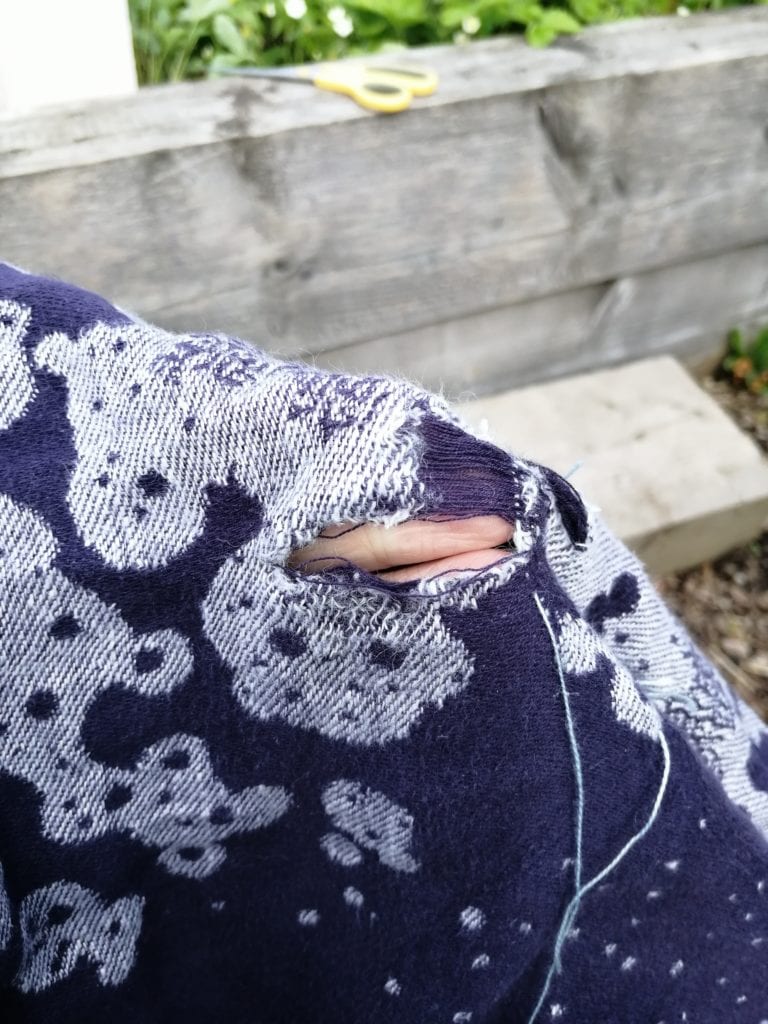
The Aim
My plan was to mend the cloth so that it could be safely used again to carry babies. I was realistic that I didn’t have the time and effort to mend it invisibly, so I just wanted the finished effect to be sympathetic to the original cloth. Had the wrap been one with a smaller, more regular pattern, I might have chosen a pretty colour (or several) to try and ‘celebrate’ the mend rather than hide it.
The Mend
As only the weft threads were missing, it was pretty much just a case of replacing them to recreate the weave structure.
First I found some yarn to use as replacement weft thread. I went for quite a thick cotton, in a shade that pretty much matched the original weft. Matching thickness didn’t matter so much, and I would recommend going for thicker rather than thinner yarn, just because it will make the process easier. Embroidery threads would be a good choice, and there tends to be a wide range of colours. You could use multiple strands to get the correct thickness for you.
After that I trimmed away the frayed weft threads. I was way too cautious with this and should have removed far more than I did at the beginning. I had to go in there with the scissors as I was working, to keep on removing more little fluffy bits. All the ‘broken’ ends just naturally settled into the cloth/ mend and nothing needed knotting. Broken threads in woven cloth are naturally just self securing, unlike in a knitted fabric which will unravel.
The darning process is explained in the videos below, but essentially I just darned the hole. I never knotted or tied any of the threads, they were all left free floating in the cloth. The nature of the weave structure means that the friction will hold them in place quite happily. Knots cause lumps and tight spots that can’t move as fluidly as the rest of the cloth (just as scar tissue can pull tight on the skin).
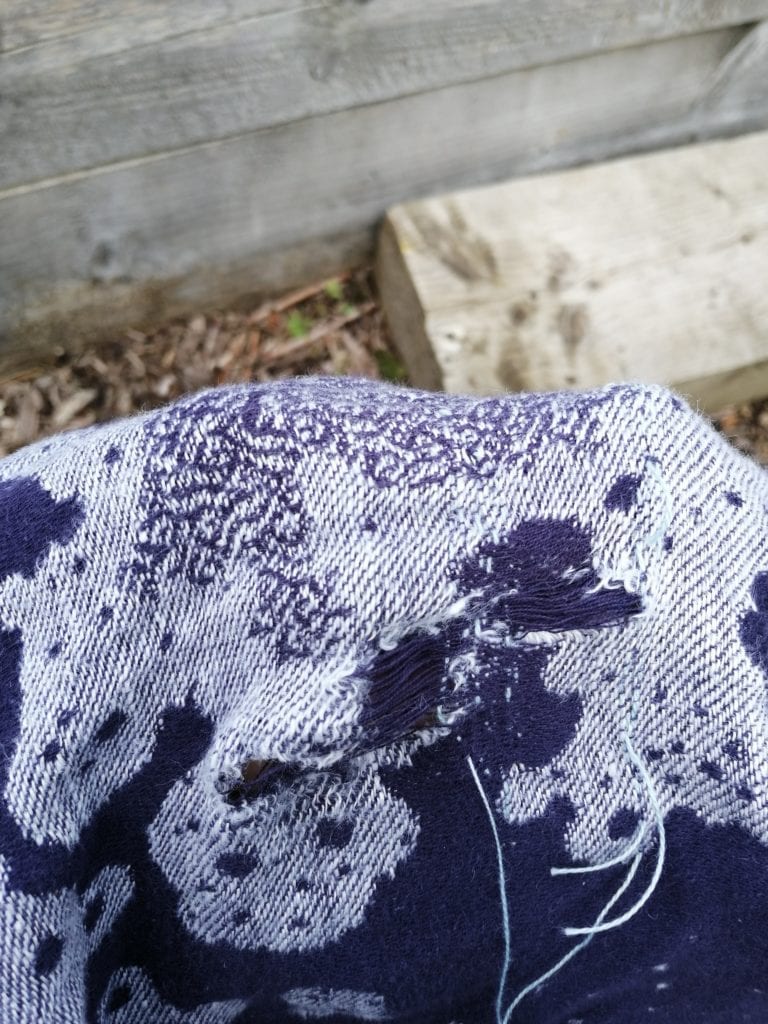
Firstly I sited a few threads at regular intervals across the hole, just to act as a bit of a scaffold and draw the warp threads back in line with each other.
Once I’d got the warp in line I started to darn, threading the needle up through the cloth in one direction, turning and working back down again. I followed the original line of each missing weft thread, making sure to take the yarn a good distance below and above the hole, into the ‘good’ cloth surrounding it.
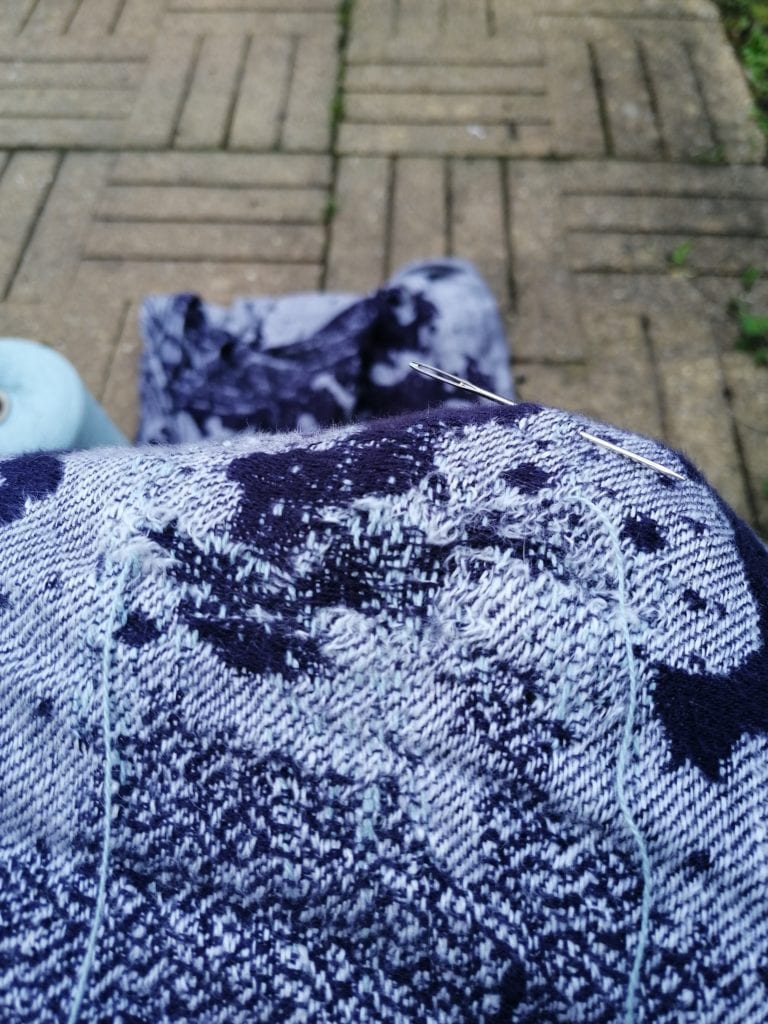
I followed the natural pattern of the cloth; essentially the path of least resistance for my needle- it was what it seemed to want to do! Once I got the open section, I used my needle to lift up a few threads at a time going under and over them in bunches. I tried to alternate this so that all those warp threads ended up quite tightly pinned.
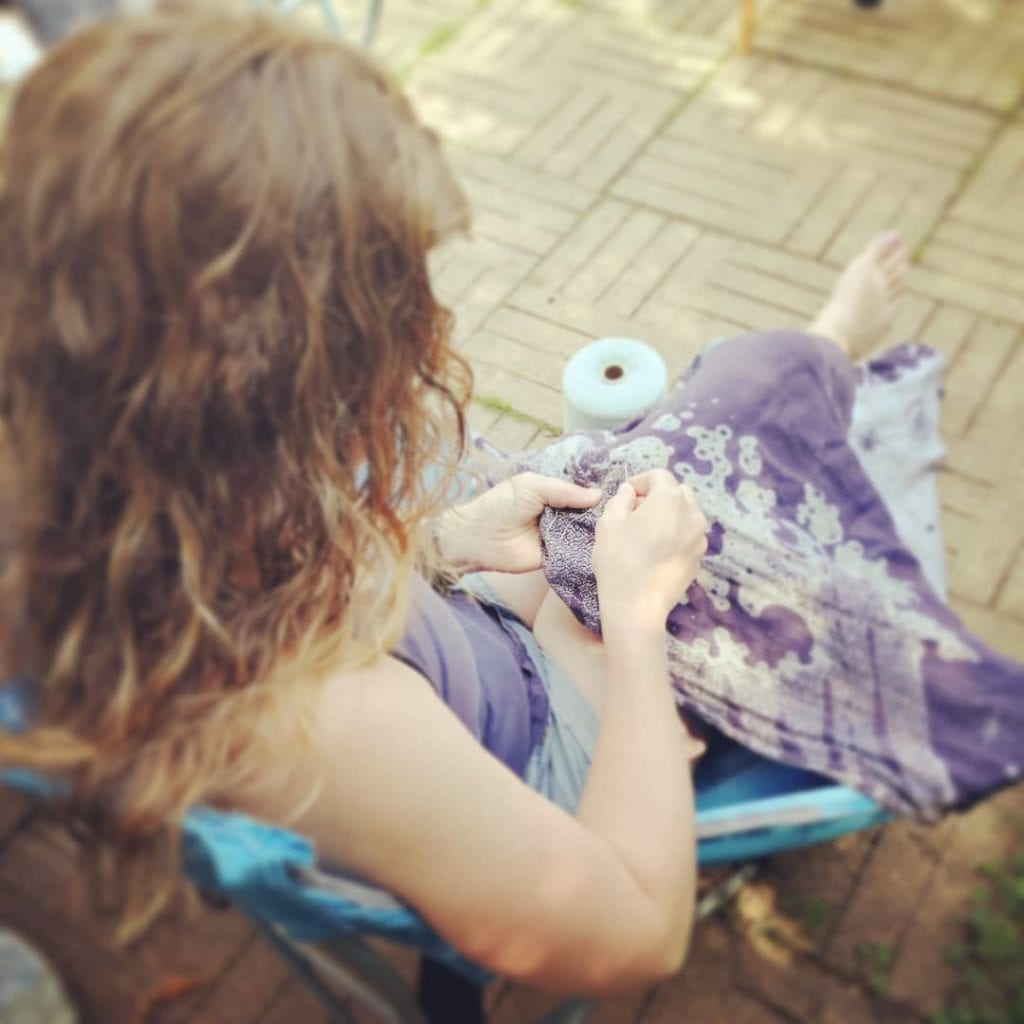
That was about it! Once I’d woven enough new thread in to close the hole completely, I went over it from the opposite side of the cloth, catching any warp threads that were floating on the surface of the cloth. I worked with lengths of thread around 40cm long at a time. At the point where I turned the yarn and started working in the opposite direction, I made sure to reenter the cloth at the same point, so that I didn’t shift any of the warp threads out of line.